Australia’s largest builder selects TrackSeal as RFID solution provider
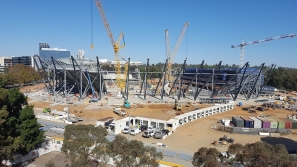
Large construction sites have many challenges such as - how many people are on site, their whereabouts, time spent on site (and in areas), what material is getting shipped by suppliers, when does it arrive, where it's get's off loaded, is the received material same as expected and dispatched, what has been fitted in the site and what is expected to be fitted within next seven days etc. Keeping track of such activities manually requires lot of manpower, even then the data available is not accurate and is not in realtime. And hence the requirement of an auto tracking and process management technology. RFID seems to be best of all and is most economical.
Below is brief on how it has been used -
The Builder had following challenges–
- How many people are on site?
- Are people on site as expected?
- Has the supplier shipped what was requested?
- Is material fabrication/assembly progress as expected?
- What material has been received and what was supposed to be received?
- Where is received material?
- Has all the received material been used up at correct places?
- Where are the delays?
- What are the bottlenecks?
The client opted to try out use of RFID and found TrackSeal to be the best solution as TrackSeal not only provides most of the features out of the box, but is able to make changes as required.
The solution monitors real time location and movements of all assets, generates alarm if a fixed asset moves out of an area, sends email if pre-programmed activity occurs and provides valuable stats to the business for process enhancements and improvements.
The solution not only provides real time visibility of all its tagged assets, but also integrates with other enterprise applications to exchange information for reducing work duplication and for keeping all data in sync.
THE GOALS
The goal of the project is to deliver the below –
- Know the progress of the material getting fabricated
- Know when it's delivered to site
- Know when it's get fitted on site and where.
- Update the backend system with the fitting details
- Provide reports and material movement to client (in realtime)
- And more
HOW IS TRACKSEAL DELIVERING THE CLIENT’S GOALS?
Proposed Hardware/Software
- Fixed reader portal at all fabrication/painting plants and at site
- Handheld scanners at all locations
- On-metal tags of different types for parts as well as for final assemblies
- iTrack software
Contact TrackSeal at info@trackseal.com or call us on +61 2 8091 0707 for further details on this solution or to provide a customized solution to automate your business processes.